Destylacja rozpuszczalników to kluczowy proces stosowany w laboratoriach chemicznych, który pozwala na oddzielenie substancji na podstawie różnicy ich temperatur wrzenia. Proces ten jest szczególnie istotny w przypadku rozpuszczalników organicznych, które często wymagają oczyszczenia przed dalszymi reakcjami chemicznymi. W laboratoriach najczęściej wykorzystuje się destylację prostą oraz destylację frakcyjną. Destylacja prosta polega na podgrzewaniu cieczy do momentu, gdy zaczyna parować, a następnie skraplaniu pary w chłodnicy. W przypadku destylacji frakcyjnej, proces ten jest bardziej złożony i polega na wielokrotnym skraplaniu i odparowywaniu, co pozwala na uzyskanie wyższej czystości produktu końcowego. Wybór metody destylacji zależy od właściwości fizycznych rozpuszczalników oraz ich mieszanin. W laboratoriach ważne jest również monitorowanie temperatury oraz ciśnienia, aby zapewnić optymalne warunki dla procesu destylacji.
Jakie są zastosowania destylacji rozpuszczalników w przemyśle
Destylacja rozpuszczalników znajduje szerokie zastosowanie w różnych gałęziach przemysłu, w tym w przemyśle chemicznym, farmaceutycznym oraz petrochemicznym. W przemyśle chemicznym proces ten jest wykorzystywany do produkcji czystych substancji chemicznych, które są niezbędne do wytwarzania różnorodnych produktów, takich jak tworzywa sztuczne czy barwniki. W przemyśle farmaceutycznym destylacja odgrywa kluczową rolę w oczyszczaniu składników aktywnych leków, co ma bezpośredni wpływ na ich skuteczność oraz bezpieczeństwo stosowania. Z kolei w przemyśle petrochemicznym destylacja jest podstawową metodą separacji różnych frakcji ropy naftowej, co pozwala na uzyskanie paliw oraz innych produktów chemicznych. Proces ten umożliwia także recykling rozpuszczalników, co przyczynia się do zmniejszenia kosztów produkcji oraz ochrony środowiska.
Jakie są różnice między destylacją prostą a frakcyjną
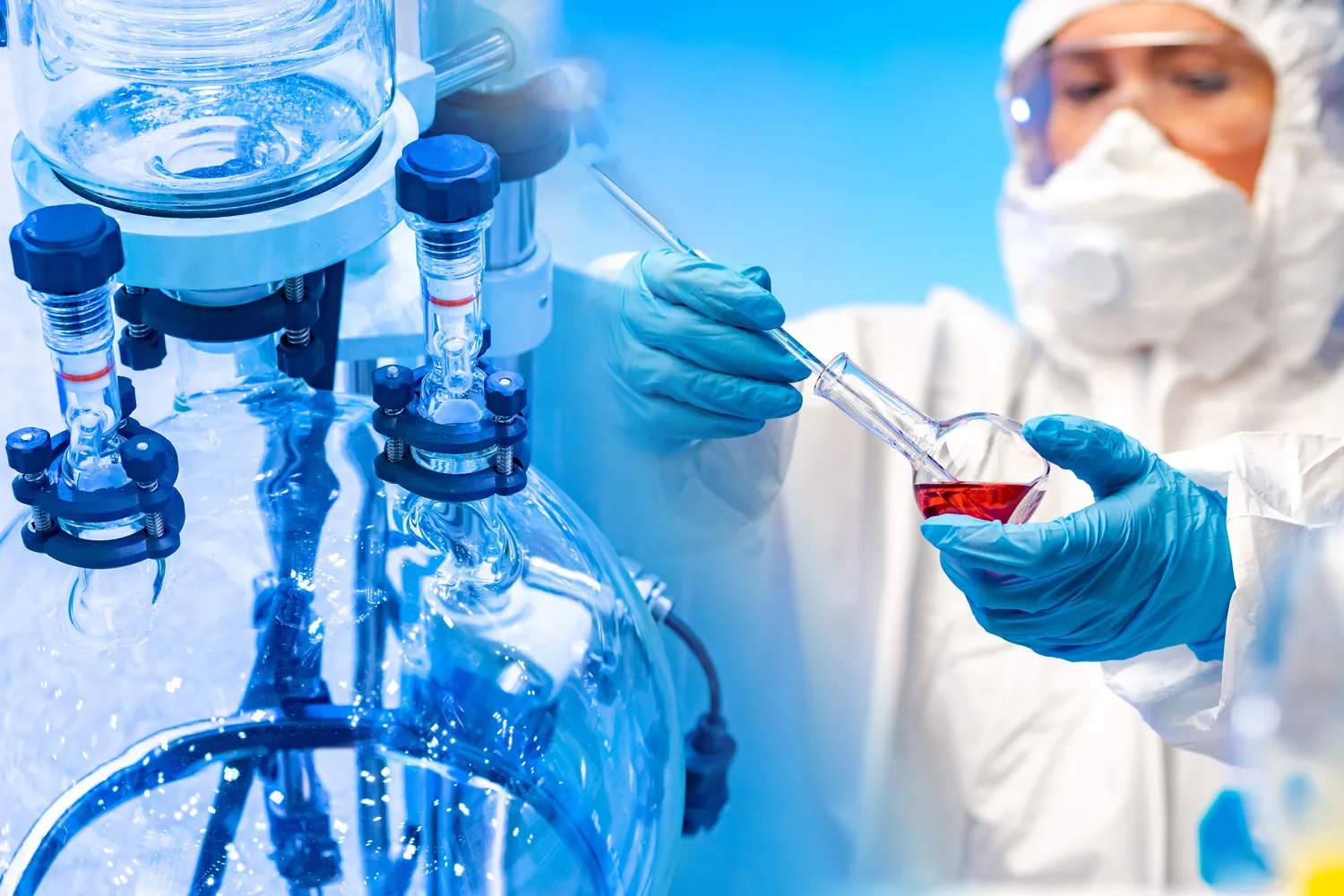
Destylacja prosta i frakcyjna to dwie podstawowe metody separacji substancji na podstawie różnicy temperatur wrzenia, jednak różnią się one znacznie pod względem zastosowania oraz efektywności. Destylacja prosta jest najczęściej stosowana w przypadku jednorodnych mieszanin cieczy o znacznej różnicy temperatur wrzenia. Proces ten jest stosunkowo prosty i polega na podgrzewaniu cieczy do momentu jej odparowania, a następnie skraplaniu pary w chłodnicy. Z kolei destylacja frakcyjna jest bardziej skomplikowana i wymaga użycia kolumny frakcyjnej, która umożliwia wielokrotne skraplanie i odparowywanie cieczy. Dzięki temu możliwe jest uzyskanie wyższej czystości produktów końcowych oraz separacja substancji o zbliżonych temperaturach wrzenia. W praktyce wybór metody zależy od charakterystyki mieszaniny oraz pożądanej czystości produktu końcowego.
Jakie sprzęty są niezbędne do przeprowadzenia destylacji rozpuszczalników
Aby przeprowadzić skuteczną destylację rozpuszczalników, niezbędne jest odpowiednie wyposażenie laboratoryjne. Podstawowym elementem jest aparat destylacyjny, który może mieć formę prostego zestawu składającego się z kolby destylacyjnej, chłodnicy oraz odbieracza. Kolba destylacyjna służy do podgrzewania cieczy, a chłodnica odpowiada za skraplanie pary wodnej powracającej do stanu ciekłego. Dodatkowo warto zaopatrzyć się w termometr do monitorowania temperatury wrzenia substancji oraz manometr do pomiaru ciśnienia wewnętrznego aparatu. W przypadku bardziej zaawansowanej destylacji frakcyjnej konieczne będzie użycie kolumny frakcyjnej, która zwiększa efektywność separacji dzięki wielokrotnemu skraplaniu i odparowywaniu cieczy. Oprócz tego przydatne mogą być także urządzenia takie jak pompy próżniowe czy systemy chłodzenia wodą lub powietrzem.
Jakie są najczęstsze błędy podczas destylacji rozpuszczalników
Podczas przeprowadzania destylacji rozpuszczalników, zarówno w laboratoriach, jak i w przemyśle, mogą wystąpić różne błędy, które wpływają na jakość uzyskiwanych produktów. Jednym z najczęstszych problemów jest niewłaściwe ustawienie temperatury. Zbyt niska temperatura może prowadzić do niepełnego odparowania substancji, co skutkuje zanieczyszczeniem końcowego produktu. Z kolei zbyt wysoka temperatura może spowodować rozkład termiczny substancji, co również negatywnie wpływa na czystość. Innym powszechnym błędem jest niewłaściwe dobranie sprzętu do specyfiki procesu. Użycie kolumny frakcyjnej o niewłaściwej wysokości lub średnicy może ograniczyć efektywność separacji. Ponadto, nieodpowiednie chłodzenie pary może prowadzić do kondensacji niepożądanych substancji. Ważne jest także monitorowanie ciśnienia wewnętrznego aparatu destylacyjnego, ponieważ jego zmiany mogą wpływać na temperatury wrzenia substancji. Warto również pamiętać o odpowiednim przygotowaniu rozpuszczalników przed destylacją, aby uniknąć zanieczyszczeń, które mogą wpłynąć na wyniki procesu.
Jakie są korzyści z zastosowania destylacji rozpuszczalników
Destylacja rozpuszczalników niesie ze sobą wiele korzyści zarówno w kontekście badań laboratoryjnych, jak i przemysłowych zastosowań. Przede wszystkim pozwala na uzyskanie wysokiej czystości substancji chemicznych, co jest kluczowe dla wielu procesów produkcyjnych oraz badań naukowych. Dzięki temu możliwe jest przeprowadzanie reakcji chemicznych z większą precyzją i efektywnością. Kolejną zaletą jest możliwość recyklingu rozpuszczalników, co przyczynia się do zmniejszenia kosztów produkcji oraz ograniczenia negatywnego wpływu na środowisko. Wiele firm stawia obecnie na zrównoważony rozwój, a efektywne wykorzystanie rozpuszczalników wpisuje się w te trendy. Destylacja pozwala również na separację substancji o podobnych właściwościach fizycznych, co jest istotne w przypadku skomplikowanych mieszanin chemicznych. Dodatkowo nowoczesne technologie destylacyjne umożliwiają automatyzację procesu, co zwiększa jego wydajność oraz bezpieczeństwo pracy w laboratoriach i zakładach przemysłowych.
Jakie są nowoczesne technologie stosowane w destylacji rozpuszczalników
W ostatnich latach rozwój technologii destylacyjnych znacząco wpłynął na efektywność i bezpieczeństwo tego procesu. Nowoczesne aparaty destylacyjne często wyposażone są w zaawansowane systemy automatyzacji, które umożliwiają precyzyjne kontrolowanie parametrów takich jak temperatura czy ciśnienie. Dzięki temu możliwe jest uzyskanie wyższej czystości produktów oraz minimalizacja ryzyka wystąpienia błędów ludzkich. Wprowadzenie technologii próżniowej pozwala na obniżenie temperatury wrzenia substancji, co jest szczególnie istotne w przypadku termolabilnych składników chemicznych. Oprócz tego nowoczesne kolumny frakcyjne charakteryzują się lepszymi właściwościami separacyjnymi dzięki zastosowaniu materiałów o wysokiej powierzchni kontaktu oraz innowacyjnych konstrukcji wewnętrznych. Warto również zwrócić uwagę na rozwój technologii membranowych, które stanowią alternatywę dla tradycyjnej destylacji i pozwalają na separację substancji przy niższych kosztach energetycznych.
Jakie są różnice między destylacją a innymi metodami separacji
Destylacja to jedna z wielu metod separacji substancji chemicznych, jednak różni się ona od innych technik pod względem zasad działania oraz zastosowań. Na przykład ekstrakcja to proces polegający na wydobywaniu składników z mieszaniny za pomocą rozpuszczalnika, który selektywnie oddziałuje z poszukiwanym związkiem chemicznym. W przeciwieństwie do destylacji, ekstrakcja nie opiera się na różnicy temperatur wrzenia, lecz na różnicach w rozpuszczalności substancji w różnych fazach. Inną popularną metodą separacji jest chromatografia, która polega na rozdzielaniu składników mieszaniny poprzez ich interakcję z fazą stacjonarną i ruchomą. Chromatografia może być bardziej skuteczna w przypadku bardzo skomplikowanych mieszanin lub gdy wymagane są ekstremalne poziomy czystości. Z drugiej strony destylacja jest bardziej odpowiednia dla jednorodnych cieczy o znacznej różnicy temperatur wrzenia.
Jakie są przyszłe kierunki rozwoju technologii destylacji
Przyszłość technologii destylacji zapowiada się obiecująco dzięki ciągłemu postępowi naukowemu oraz technologicznemu. W miarę rosnącej potrzeby ochrony środowiska oraz efektywności energetycznej coraz większą uwagę przykłada się do opracowywania innowacyjnych metod separacji i oczyszczania substancji chemicznych. Jednym z kierunków rozwoju jest integracja technologii destylacyjnych z odnawialnymi źródłami energii, co pozwoli na zmniejszenie zużycia energii podczas procesu destylacji. Dodatkowo rozwój nanotechnologii może przyczynić się do powstania nowych materiałów filtracyjnych oraz kolumn frakcyjnych o lepszych właściwościach separacyjnych. Warto również zauważyć rosnącą rolę automatyzacji i sztucznej inteligencji w procesach przemysłowych, co może zwiększyć precyzję i bezpieczeństwo operacji związanych z destylacją.
Jakie są wyzwania związane z destylacją rozpuszczalników
Mimo licznych korzyści płynących z zastosowania destylacji rozpuszczalników istnieje wiele wyzwań związanych z tym procesem. Jednym z głównych problemów jest konieczność zapewnienia wysokiej jakości surowców wejściowych, ponieważ obecność zanieczyszczeń może znacząco wpłynąć na wyniki procesu destylacji oraz jakość uzyskanych produktów końcowych. Kolejnym wyzwaniem jest optymalizacja warunków pracy aparatu destylacyjnego tak, aby maksymalizować wydajność przy minimalizacji zużycia energii i czasu pracy urządzeń. W kontekście ochrony środowiska istotnym zagadnieniem staje się także odpowiednie zarządzanie odpadami powstałymi podczas procesu destylacji oraz recykling użytych rozpuszczalników. Dodatkowo zmiany regulacyjne dotyczące stosowania substancji chemicznych mogą wpłynąć na dostępność niektórych materiałów wykorzystywanych w procesach przemysłowych.