Budowa maszyn pneumatycznych opiera się na kilku kluczowych elementach, które współpracują ze sobą w celu efektywnego wykorzystania energii sprężonego powietrza. Podstawowym komponentem jest sprężarka, która odpowiada za wytwarzanie sprężonego powietrza. Sprężarki mogą mieć różne typy, w tym tłokowe, śrubowe czy wirnikowe, a ich wybór zależy od specyficznych potrzeb aplikacji. Kolejnym istotnym elementem są zbiorniki na sprężone powietrze, które gromadzą energię i zapewniają jej stabilne dostarczanie do systemu. W maszynach pneumatycznych niezbędne są także zawory, które kontrolują przepływ powietrza oraz jego kierunek. Zawory te mogą być ręczne lub automatyczne, co wpływa na wygodę i efektywność obsługi. Ważnym aspektem budowy maszyn pneumatycznych są również siłowniki, które przekształcają energię sprężonego powietrza na ruch mechaniczny. Siłowniki mogą mieć różne kształty i rozmiary, a ich dobór jest kluczowy dla osiągnięcia zamierzonych rezultatów w danym procesie technologicznym.
Jakie zastosowania mają maszyny pneumatyczne w przemyśle
Maszyny pneumatyczne znajdują szerokie zastosowanie w różnych gałęziach przemysłu dzięki swojej wszechstronności i efektywności. W sektorze produkcyjnym często wykorzystuje się je do automatyzacji procesów montażowych oraz pakowania. Dzięki zastosowaniu siłowników pneumatycznych możliwe jest szybkie i precyzyjne wykonywanie operacji takich jak podnoszenie, przesuwanie czy wciskanie elementów. W branży motoryzacyjnej maszyny pneumatyczne są wykorzystywane do lakierowania pojazdów oraz do obsługi narzędzi pneumatycznych, co znacząco przyspiesza proces produkcji. W logistyce i magazynowaniu maszyny te służą do transportu materiałów oraz ich sortowania, co zwiększa efektywność pracy. W sektorze spożywczym maszyny pneumatyczne są stosowane do pakowania produktów oraz ich transportu w linii produkcyjnej, co zapewnia zachowanie wysokich standardów higieny. Ponadto, w medycynie maszyny pneumatyczne wspierają różnorodne procesy związane z diagnostyką oraz leczeniem pacjentów.
Jakie są zalety i wady maszyn pneumatycznych
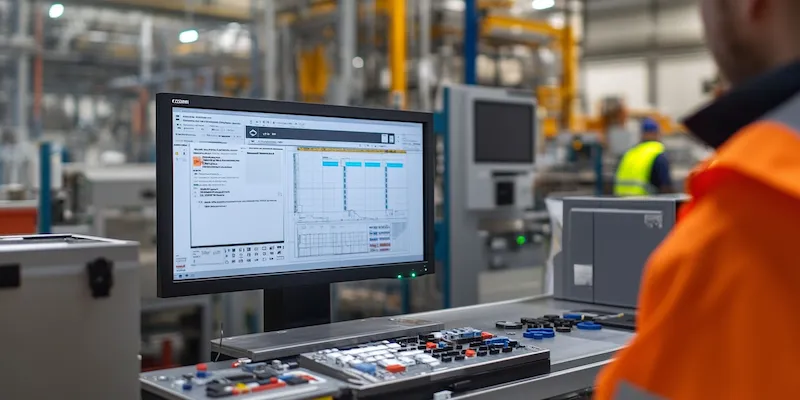
Maszyny pneumatyczne charakteryzują się wieloma zaletami, które sprawiają, że są one chętnie wykorzystywane w różnych aplikacjach przemysłowych. Przede wszystkim ich konstrukcja jest stosunkowo prosta, co ułatwia konserwację oraz naprawy. Dodatkowo maszyny te oferują dużą moc przy niewielkiej wadze, co pozwala na ich łatwe przenoszenie oraz instalację w różnych miejscach. Pneumatyka jest również bezpieczna dla użytkowników, ponieważ nie generuje iskier ani nie wymaga stosowania substancji chemicznych, co minimalizuje ryzyko pożaru czy wybuchu. Jednakże istnieją także pewne ograniczenia związane z używaniem maszyn pneumatycznych. Jednym z głównych problemów jest konieczność dostarczania sprężonego powietrza z zewnętrznych źródeł, co może wiązać się z dodatkowymi kosztami związanymi z eksploatacją sprężarek oraz systemów dystrybucji powietrza. Ponadto efektywność energetyczna maszyn pneumatycznych może być niższa w porównaniu do innych technologii, takich jak hydraulika czy elektryka.
Jakie nowoczesne technologie wspierają budowę maszyn pneumatycznych
W ostatnich latach rozwój technologii znacząco wpłynął na budowę maszyn pneumatycznych oraz ich funkcjonalność. Nowoczesne systemy sterowania umożliwiają precyzyjne zarządzanie pracą siłowników oraz zaworów, co przekłada się na większą dokładność operacji oraz oszczędność energii. Technologie takie jak Internet rzeczy (IoT) pozwalają na monitorowanie pracy maszyn w czasie rzeczywistym oraz zbieranie danych dotyczących ich wydajności. Dzięki temu możliwe jest szybsze diagnozowanie problemów oraz optymalizacja procesów produkcyjnych. Dodatkowo zastosowanie materiałów kompozytowych i lekkich stopów metali w konstrukcji maszyn pneumatycznych przyczynia się do zmniejszenia ich wagi oraz zwiększenia odporności na korozję. Wprowadzenie rozwiązań automatyzacyjnych takich jak robotyka współpracująca (cobots) umożliwia integrację maszyn pneumatycznych z innymi systemami produkcyjnymi, co zwiększa elastyczność linii produkcyjnych. Również rozwój technologii filtracji i osuszania powietrza przyczynia się do poprawy jakości medium roboczego oraz wydajności całego układu.
Jakie są kluczowe różnice między pneumatycznymi a hydraulicznymi maszynami
Wybór między maszynami pneumatycznymi a hydraulicznymi często zależy od specyfiki zastosowania oraz wymagań dotyczących wydajności i precyzji. Jedną z głównych różnic jest medium robocze, które w przypadku maszyn pneumatycznych stanowi sprężone powietrze, podczas gdy w hydraulice wykorzystywane są płyny, najczęściej oleje. Ta różnica wpływa na charakterystykę działania obu systemów. Maszyny pneumatyczne są zazwyczaj lżejsze i prostsze w budowie, co ułatwia ich transport oraz instalację. Z drugiej strony, systemy hydrauliczne oferują większą siłę i moment obrotowy, co czyni je bardziej odpowiednimi do cięższych aplikacji wymagających dużej mocy. W kontekście szybkości działania, maszyny pneumatyczne mogą osiągać wyższe prędkości ruchu, co jest korzystne w procesach wymagających szybkiej reakcji. Jednakże w przypadku precyzyjnego sterowania ruchem, hydraulika może zapewnić lepszą dokładność dzięki możliwości regulacji ciśnienia płynu. Kolejnym aspektem jest koszt eksploatacji; sprężone powietrze jest łatwiejsze do uzyskania i tańsze w utrzymaniu niż olej hydrauliczny, co może wpływać na decyzję o wyborze jednego z tych rozwiązań.
Jakie są najczęstsze problemy związane z maszynami pneumatycznymi
Maszyny pneumatyczne, mimo swoich licznych zalet, mogą napotykać różne problemy, które wpływają na ich wydajność oraz niezawodność. Jednym z najczęstszych problemów jest wyciek sprężonego powietrza, który może prowadzić do znacznych strat energii oraz obniżenia efektywności całego systemu. Wyciek może występować w różnych miejscach, takich jak połączenia rur czy uszczelki, dlatego regularna kontrola stanu technicznego jest niezbędna. Kolejnym problemem mogą być zanieczyszczenia w sprężonym powietrzu, które mogą prowadzić do uszkodzeń elementów układu oraz obniżenia jakości produkcji. Dlatego istotne jest stosowanie odpowiednich filtrów i osuszaczy powietrza. Inne trudności to niewłaściwe ustawienia ciśnienia roboczego, które mogą powodować nieprawidłowe działanie siłowników lub zaworów. Zbyt niskie ciśnienie może skutkować brakiem mocy, podczas gdy zbyt wysokie może prowadzić do uszkodzeń komponentów. Warto także zwrócić uwagę na zużycie części mechanicznych; regularna konserwacja i wymiana zużytych elementów są kluczowe dla zapewnienia długotrwałej i bezawaryjnej pracy maszyn pneumatycznych.
Jakie są przyszłe kierunki rozwoju technologii maszyn pneumatycznych
Przyszłość technologii maszyn pneumatycznych zapowiada się obiecująco dzięki ciągłemu postępowi w dziedzinie automatyzacji oraz cyfryzacji przemysłu. W miarę jak przemysł 4.0 nabiera tempa, coraz większą rolę odgrywają inteligentne systemy zarządzania produkcją, które integrują maszyny pneumatyczne z innymi technologiami. Wprowadzenie sztucznej inteligencji do procesów sterowania pozwala na optymalizację pracy maszyn oraz przewidywanie potencjalnych awarii zanim one wystąpią. Dodatkowo rozwój technologii IoT umożliwia zbieranie danych z maszyn w czasie rzeczywistym, co pozwala na lepszą analizę ich wydajności oraz identyfikację obszarów do poprawy. W kontekście ekologii rośnie również zainteresowanie rozwiązaniami zmniejszającymi zużycie energii oraz emisję hałasu związanych z pracą maszyn pneumatycznych. Nowoczesne materiały i technologie produkcji przyczyniają się do zwiększenia efektywności energetycznej oraz trwałości komponentów. Również rozwój systemów regeneracyjnych pozwala na odzyskiwanie energii ze sprężonego powietrza, co może znacząco wpłynąć na koszty eksploatacji.
Jakie są kluczowe czynniki wpływające na wybór maszyn pneumatycznych
Wybór odpowiednich maszyn pneumatycznych do konkretnego zastosowania wymaga uwzględnienia wielu czynników, które mogą znacząco wpłynąć na efektywność pracy oraz koszty eksploatacji. Przede wszystkim należy określić wymagania dotyczące mocy i wydajności urządzenia; różne aplikacje mogą wymagać różnych parametrów technicznych, takich jak ciśnienie robocze czy przepływ powietrza. Ważnym aspektem jest także dostępność sprężonego powietrza; jeśli system nie jest w stanie dostarczyć odpowiedniej ilości medium roboczego, wydajność maszyny będzie ograniczona. Kolejnym czynnikiem jest środowisko pracy; w przypadku aplikacji w trudnych warunkach atmosferycznych należy wybrać maszyny o podwyższonej odporności na korozję czy zanieczyszczenia. Koszt zakupu i eksploatacji również odgrywa kluczową rolę; warto uwzględnić zarówno cenę samego urządzenia, jak i koszty związane z jego utrzymaniem oraz ewentualnymi naprawami. Dodatkowo istotne jest wsparcie techniczne oraz dostępność części zamiennych; wybierając producenta maszyn pneumatycznych warto zwrócić uwagę na jego renomę oraz jakość oferowanych usług serwisowych.
Jakie są najlepsze praktyki konserwacji maszyn pneumatycznych
Aby zapewnić długotrwałą i bezawaryjną pracę maszyn pneumatycznych, niezwykle istotne jest przestrzeganie najlepszych praktyk konserwacyjnych. Regularna kontrola stanu technicznego urządzeń pozwala na wczesne wykrywanie potencjalnych problemów i ich szybkie usuwanie przed wystąpieniem poważniejszych awarii. Kluczowym elementem konserwacji jest czyszczenie filtrów powietrza oraz osuszaczy; ich prawidłowe funkcjonowanie ma ogromny wpływ na jakość medium roboczego oraz wydajność całego układu. Należy również regularnie sprawdzać szczelność połączeń rur oraz uszczelek; wszelkie wycieki należy natychmiast naprawić, aby uniknąć strat energii i obniżenia efektywności pracy maszyny. Warto także kontrolować poziom oleju w sprężarkach oraz innych elementach wymagających smarowania; niewłaściwe smarowanie może prowadzić do szybszego zużycia komponentów i zwiększenia ryzyka awarii. Dodatkowo zaleca się prowadzenie dokumentacji dotyczącej przeprowadzonych przeglądów i napraw; pozwala to na lepsze planowanie działań konserwacyjnych oraz identyfikację trendów dotyczących zużycia poszczególnych elementów maszyny.