Destylator przemysłowy to urządzenie, które służy do oddzielania składników mieszanin cieczy na podstawie różnic w ich temperaturze wrzenia. W procesie destylacji ciecz jest podgrzewana, a następnie para, która powstaje, jest schładzana i skraplana, co pozwala na uzyskanie czystego produktu. W przemyśle destylatory są wykorzystywane w różnych dziedzinach, takich jak chemia, petrochemia czy produkcja alkoholu. Istnieje wiele rodzajów destylatorów, w tym destylatory prostokątne, kolumnowe oraz frakcyjne, które różnią się konstrukcją i zastosowaniem. W przypadku destylacji frakcyjnej możliwe jest oddzielanie wielu składników jednocześnie, co czyni ten proces bardziej efektywnym. Destylatory przemysłowe są zazwyczaj dużych rozmiarów i mogą obsługiwać znaczne ilości cieczy, co sprawia, że są kluczowym elementem w wielu procesach produkcyjnych.
Jakie są zastosowania destylatorów przemysłowych w różnych branżach?
Destylatory przemysłowe znajdują szerokie zastosowanie w wielu branżach, co czyni je niezwykle wszechstronnymi urządzeniami. W przemyśle chemicznym są one wykorzystywane do oczyszczania surowców oraz produkcji różnych substancji chemicznych. Na przykład w produkcji alkoholu destylatory pozwalają na uzyskanie wysokoprocentowych napojów poprzez oddzielanie etanolu od innych składników. W branży petrochemicznej destylatory służą do przetwarzania ropy naftowej, gdzie różne frakcje są oddzielane w zależności od ich temperatury wrzenia. Ponadto w przemyśle farmaceutycznym destylacja jest kluczowym procesem przy produkcji leków oraz substancji czynnych. Zastosowanie destylatorów obejmuje również oczyszczanie wody oraz produkcję biopaliw, co staje się coraz bardziej istotne w kontekście ochrony środowiska.
Jakie są kluczowe elementy konstrukcyjne destylatora przemysłowego?
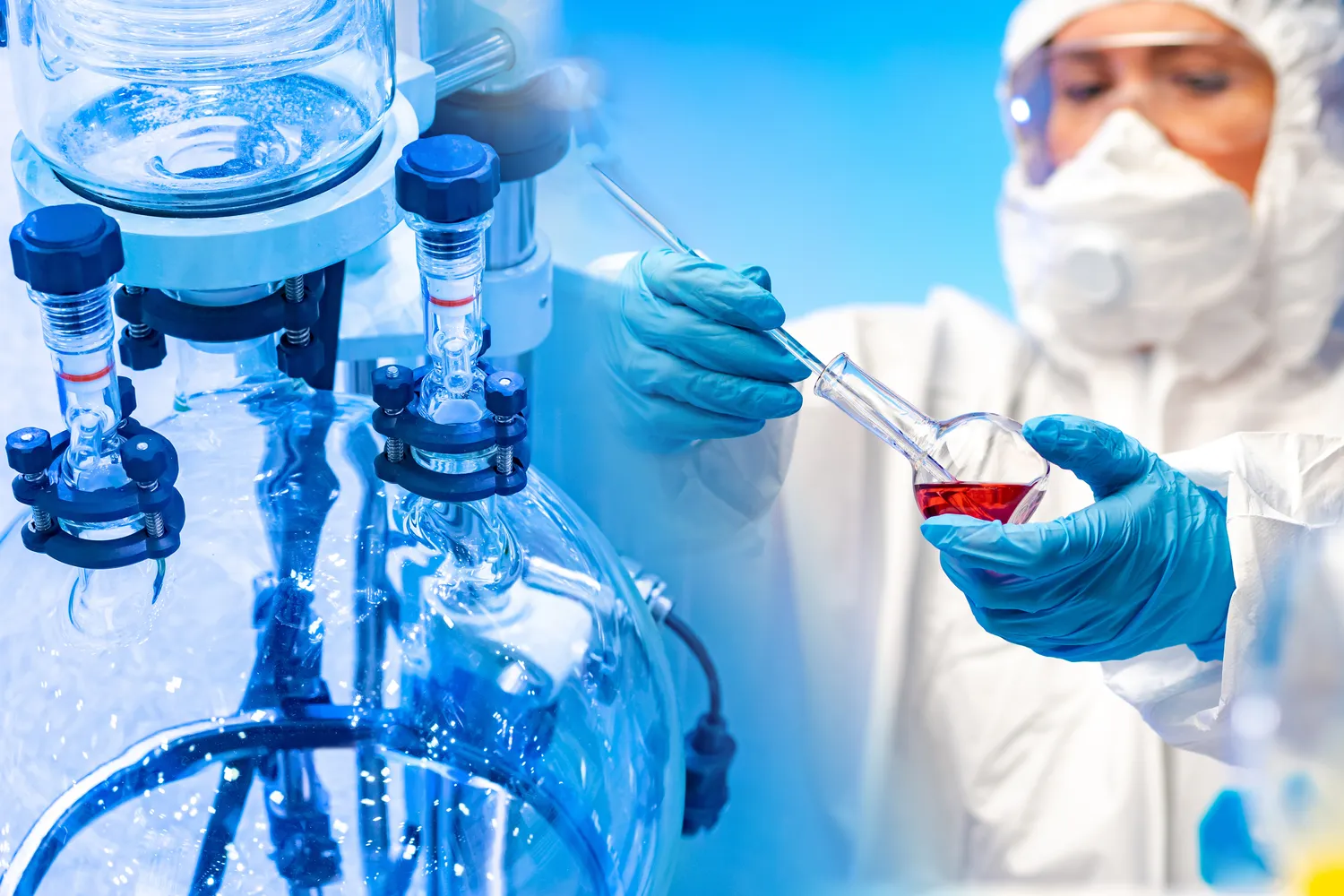
Konstrukcja destylatora przemysłowego składa się z kilku kluczowych elementów, które zapewniają jego prawidłowe działanie oraz efektywność procesu destylacji. Podstawowym elementem jest zbiornik do podgrzewania cieczy, który może być wyposażony w różnego rodzaju źródła ciepła, takie jak palniki gazowe lub elektryczne grzałki. Następnie para powstała podczas podgrzewania przechodzi przez kolumnę destylacyjną, gdzie następuje jej schłodzenie i kondensacja. Kolumna ta może być wyposażona w różne elementy takie jak półki czy packingi, które zwiększają powierzchnię kontaktu między parą a cieczą, co poprawia efektywność separacji składników. Kolejnym ważnym elementem jest skraplacz, który umożliwia schłodzenie pary i jej skroplenie do postaci cieczy. Oprócz tego destylatory często mają systemy monitorujące temperaturę oraz ciśnienie wewnętrzne, co pozwala na optymalizację procesu oraz zwiększenie bezpieczeństwa pracy urządzenia.
Jakie są najnowsze technologie stosowane w destylatorach przemysłowych?
W ostatnich latach rozwój technologii znacząco wpłynął na konstrukcję i funkcjonalność destylatorów przemysłowych. Nowoczesne urządzenia często wykorzystują zaawansowane systemy automatyzacji, które pozwalają na zdalne monitorowanie i kontrolowanie procesu destylacji. Dzięki temu operatorzy mogą szybko reagować na zmiany warunków pracy oraz optymalizować parametry procesu w czasie rzeczywistym. Ponadto wiele nowoczesnych destylatorów wyposażonych jest w technologie odzysku ciepła, co pozwala na znaczne oszczędności energetyczne i zmniejszenie kosztów operacyjnych. Innowacyjne materiały używane do budowy kolumn czy skraplaczy zwiększają efektywność separacji oraz odporność na korozję. Wprowadzenie sztucznej inteligencji do analizy danych z procesu pozwala na lepsze prognozowanie wyników oraz identyfikację potencjalnych problemów zanim staną się one krytyczne.
Jakie są kluczowe czynniki wpływające na efektywność destylacji?
Efektywność procesu destylacji w destylatorach przemysłowych zależy od wielu czynników, które mogą znacząco wpłynąć na jakość uzyskiwanego produktu oraz wydajność całego procesu. Jednym z najważniejszych elementów jest temperatura, która musi być odpowiednio dobrana do rodzaju cieczy oraz składników, które mają być oddzielone. Zbyt wysoka temperatura może prowadzić do niepożądanych reakcji chemicznych, natomiast zbyt niska może skutkować niepełnym oddzieleniem składników. Kolejnym istotnym czynnikiem jest ciśnienie, które również wpływa na temperaturę wrzenia cieczy. W niektórych przypadkach stosuje się destylację pod zmniejszonym ciśnieniem, co pozwala na obniżenie temperatury wrzenia i minimalizację degradacji termicznej wrażliwych substancji. Ważne są także parametry konstrukcyjne samego destylatora, takie jak wysokość kolumny czy rodzaj zastosowanych elementów separacyjnych. Odpowiedni dobór tych parametrów pozwala na zwiększenie powierzchni kontaktu między parą a cieczą, co przekłada się na lepszą efektywność separacji.
Jakie są najczęstsze problemy związane z eksploatacją destylatorów przemysłowych?
Podczas eksploatacji destylatorów przemysłowych mogą występować różnorodne problemy, które mogą wpływać na efektywność i bezpieczeństwo pracy urządzenia. Jednym z najczęstszych problemów jest osadzanie się zanieczyszczeń w kolumnach destylacyjnych, co prowadzi do zmniejszenia efektywności separacji oraz konieczności częstszego czyszczenia urządzenia. Osady te mogą pochodzić zarówno z surowców, jak i z procesów chemicznych zachodzących w trakcie destylacji. Innym problemem może być niewłaściwe ustawienie parametrów pracy, takich jak temperatura czy ciśnienie, co może prowadzić do niepełnego oddzielenia składników lub ich degradacji. Również awarie systemów monitorujących mogą skutkować brakiem kontroli nad procesem, co zwiększa ryzyko wystąpienia niebezpiecznych sytuacji. W przypadku destylatorów wykorzystywanych w przemyśle chemicznym należy również zwrócić uwagę na kwestie związane z bezpieczeństwem pracy – wycieki substancji chemicznych czy problemy z wentylacją mogą stwarzać zagrożenie dla pracowników oraz środowiska.
Jakie są koszty związane z inwestycją w destylatory przemysłowe?
Inwestycja w destylatory przemysłowe wiąże się z różnorodnymi kosztami, które należy uwzględnić przy planowaniu zakupu i eksploatacji tych urządzeń. Koszt zakupu samego destylatora może być znaczny i zależy od jego wielkości, rodzaju oraz zastosowanych technologii. Nowoczesne destylatory wyposażone w zaawansowane systemy automatyzacji oraz energooszczędne rozwiązania będą droższe niż tradycyjne modele. Dodatkowo należy uwzględnić koszty związane z instalacją urządzenia oraz ewentualnymi modyfikacjami infrastruktury zakładu produkcyjnego. Koszty eksploatacyjne obejmują zużycie energii, która jest kluczowym czynnikiem wpływającym na rentowność procesu destylacji. Warto również pamiętać o kosztach związanych z konserwacją i serwisowaniem urządzenia, które są niezbędne dla zapewnienia jego długotrwałej i bezawaryjnej pracy. W przypadku awarii lub konieczności wymiany części zamiennych mogą wystąpić dodatkowe wydatki.
Jakie są przyszłe kierunki rozwoju technologii destylacyjnych?
Przyszłość technologii destylacyjnych zapowiada się bardzo obiecująco, a wiele innowacyjnych rozwiązań może znacząco wpłynąć na efektywność i bezpieczeństwo procesów przemysłowych. Jednym z głównych kierunków rozwoju jest automatyzacja procesów, która pozwala na bardziej precyzyjne kontrolowanie parametrów pracy oraz szybsze reagowanie na zmiany warunków operacyjnych. Wprowadzenie sztucznej inteligencji do analizy danych umożliwia optymalizację procesów oraz przewidywanie potencjalnych problemów zanim staną się one krytyczne. Kolejnym trendem jest rozwój technologii odzysku ciepła, co pozwala na znaczne oszczędności energetyczne i zmniejszenie kosztów operacyjnych. Coraz większą uwagę przykłada się także do kwestii ekologicznych – nowoczesne destylatory będą musiały spełniać coraz bardziej rygorystyczne normy dotyczące emisji oraz zużycia zasobów naturalnych. Innowacyjne materiały używane do budowy kolumn czy skraplaczy zwiększą efektywność separacji oraz odporność na korozję.
Jakie są różnice między destylacją prostą a frakcyjną?
Destylacja prosta i frakcyjna to dwa podstawowe rodzaje procesów stosowanych w destylatorach przemysłowych, które różnią się zarówno zasadą działania, jak i zastosowaniami. Destylacja prosta polega na jednorazowym podgrzewaniu cieczy i skraplaniu powstałej pary bez dodatkowych etapów separacji. Jest to metoda stosunkowo prosta i tania, jednak jej efektywność jest ograniczona do mieszanin zawierających niewielką liczbę składników o wyraźnie różnych temperaturach wrzenia. Z kolei destylacja frakcyjna to bardziej zaawansowany proces, który wykorzystuje kolumny destylacyjne wyposażone w elementy separacyjne takie jak półki czy packingi. Dzięki temu możliwe jest oddzielanie wielu składników jednocześnie w oparciu o ich różnice w temperaturze wrzenia. Destylacja frakcyjna jest znacznie bardziej efektywna i pozwala na uzyskanie wyższej czystości produktów końcowych, dlatego znajduje zastosowanie w przemyśle chemicznym oraz petrochemicznym przy przetwarzaniu skomplikowanych mieszanin.
Jakie są zalety korzystania z nowoczesnych destylatorów przemysłowych?
Korzystanie z nowoczesnych destylatorów przemysłowych przynosi wiele korzyści zarówno dla producentów, jak i dla środowiska naturalnego. Przede wszystkim nowoczesne urządzenia charakteryzują się wyższą efektywnością energetyczną dzięki zastosowaniu innowacyjnych technologii odzysku ciepła oraz automatyzacji procesów. To przekłada się na niższe koszty operacyjne oraz mniejsze zużycie energii elektrycznej czy paliw kopalnych. Dodatkowo nowoczesne destylatory są często wyposażone w zaawansowane systemy monitorujące parametry pracy, co pozwala na szybsze identyfikowanie problemów oraz optymalizację procesu produkcji. W rezultacie możliwe jest uzyskanie wyższej jakości produktów końcowych przy mniejszych stratach surowców. Ponadto nowoczesne technologie często uwzględniają aspekty ekologiczne – wiele nowych modeli spełnia rygorystyczne normy dotyczące emisji szkodliwych substancji do atmosfery oraz zużycia wody, co przyczynia się do ochrony środowiska naturalnego.